9月14日,在中国航天科工集团有限公司(以下简称“集团公司”)第六次质量工作会议上,湖南磁电铁氧体原材料部荣获集团公司“2015-2017年度质量工作先进集体”,这份荣誉充分肯定了湖南磁电在质量建设工作方面取得的突出成就。
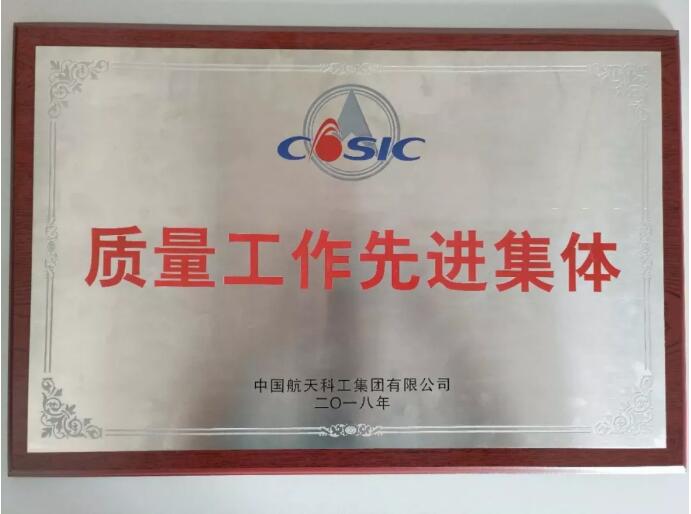
铁氧体原材料部(预烧料项目组)成立于2016年,仅用10个月的时间成功建成国内领先的两条原材料生产线,并于2016年12份批产400吨6系产品,实现了当年立项、当年建设、当年投产的目标。铁氧体原材料部也从当初3人建设小组发展到如今的20人机制健全的独立部门。技术研发小组成员平均年龄不足26周岁,先后完成7系、9系、12系高性能铁氧体原材料制备的核心技术,为公司拓展高端市场奠定了坚实基础。
2015-2017年,铁氧体原材料部牢固树立“质量至上、质量就是生命、质量就是胜算”的意识,坚持“质量第一、效率优先”的原则,圆满的完成各年度的质量目标和质量工作。
全面落实质量责任制,有效开展系统预防
全面落实质量责任制。铁氧体原材料部成立之初将质量工作做为首要工作来抓,通过确定管理架构,制定各岗位具体质量职责,落实岗位质量责任,形成了“一横到边,一纵到底”的工作网络。通过做好年度质量目标分解、每周定期召开质量工作会议的方式,不断改进质量工作方法,总结阶段性的质量管理经验,使得瓦磁产品合格率达到90%以上。同时,结合原材料生产线实际,制定《预烧料质量问题管理办法》,确保质量问题“出现必罚,罚有所依”。
纵深推进系统预防工作。工艺上,制定产品潜在失效模式及后果分析(FMEA),对构成过程的各工序逐一进行分析,找出潜在的失效模式,分析可能产生的后果,从而有效预防质量事故的发生;设备上,对于关键参数、易出问题点,建立自动化报警装置。同时,建立生产过程中“自检、互检、专检”相结合的质量制度,有效保证产品质量的稳定。
深入推进科研生产“四个两”,不断增强质量优势
坚持理念先进,以“双归零”为指导。针对生产过程中出现的质量异常情况,铁氧体原材料部采取质量、管理双归零的思路和方法进行分析,有效预防低层次质量问题重复出现,杜绝重大质量事故的发生。
着眼长远发展,大力提升自动化水平。运用自动化生产技术提升产品质量已成为磁材行业的共识。铁氧体原材料生产线主体采用管道泵送加子系统模块形式,结合重量传感器、液位计、温度传感器、压力传感器等将各工序的生产情况实时传输到计算机集散控制系统,实现生产过程可视化。同时结合XRF分析对材料成份进行精确控制,从而实现了预烧料生产过程的全质量管控。
坚持问题导向,持续优化原材料配方设。通过改进HMS-9预烧料的配方设计及烧结工艺,使HMS-9预烧料的关键指标剩磁(Br)提高2.5%、内禀矫顽力(HcJ)的波动范围由±5%缩小到±3%;通过对不同种类的铁红原料进行验证性实验,优化HMS-7预烧料的生产工艺,使HMS-7预烧料的收缩率由±1%缩小到±0.5%。产品的磁性能一致性得到大幅改善,各项指标处于国内领先地位,产品质量受到客户好评。
多方认可,质量管理工作活力增强
技术专利点上开花。铁氧体原材料部深入贯彻“设计优化要深入、工艺优化要深入”的要求,不断推动技术创新,获得多项发明专利,其中发明专利“一种提高永磁铁氧体内禀矫顽力的方法”和“一种铁氧体磁性材料及其制造方法”获得湖南省发明专利三等奖。
质量管理工作获得认可。原材料生产线运用高度自动化手段实现了质量管理与生产过程的深度融合,成效显著,获得各级单位的认可。“高性能永磁铁氧体智能生产线建设”项目2015年被列为长沙智能制造第一批试点示范项目;“高性能永磁铁氧体批产技术研发”项目2017年获得湖南省军民融合产业发展专项资金90万项目支持;“回转窑废料自动化回收系统”获得湖南航天2017年“三创新·双创秀”活动三等奖;铁氧体原料部2017年被评为“湖南航天有限责任公司青年文明号”。
|